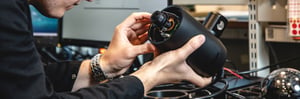
Tailored OEM & ODM Solutions
Customized products
Our experts can help you with tailored products or customized standard products to meet your specifications.
As innovative industries and companies keep pushing the development boundaries, adopting new technologies, and integrating new systems and hardware to seize future opportunities, there is an ever-growing need for task-specific, customized, and tailor-made products. Innovation means breaking the mold – both figuratively and literally – and this often means that standardized, mass-produced components simply will not cut it.
Our approach to customized products
– For the last three decades, Hatteland Technology has designed and developed a variety of customized products, from customizing standard components with new electronics or a new display to creating brand new products from the ground up. Our customers want effective solutions that are tailored to specific areas of use and that serve a specific purpose, says Frode Grindheim, VP of Products at Hatteland Technology.
– Typically, when a customer approaches us for help in solving a challenge, they don’t have a final product in mind but rather a set of requirements in terms of performance, dimensions, and I/O. They rely on our broad expertise and experience to come up with a solution, he adds.
We believe in bringing all our experts to the table and presenting them with a challenge that needs solving

Bringing all our experts to the table
Offering both OEM (Original Equipment Manufacturing) and ODM (Original Design Manufacturing) product customization, Hatteland Technology develops and manufactures tailor-made products in-house at a facility in Aksdal, Norway, often aided by modules and components supplied by trusted providers.
To deliver the best product possible, Hatteland draws on expert knowledge from the entire value chain – be it our own R&D resources, suppliers, trusted partners, senior industrial consultants at the Taiwan office, or experienced engineers at the Swedish sister company QRTECH.
– We believe in bringing all our experts to the table and presenting them with a challenge that needs solving. At Hatteland Technology, we work closely with leading companies across a wide array of industries and utilize their expertise whether we are developing our own products or meeting a customer’s requirements, says Grindheim.
–Based on a customer’s idea, need, or technical specification, we strongly believe in working together with the customer to develop the best possible solution, Grindheim adds.
Why choose Hatteland Technology?
The process
Concept
The first step in the development process is the concept phase. This is where the customer presents Hatteland Technology with an idea, a request or a challenge, and the work begins to find a solution with detailed specifications and an accompanying project charter.The output of the concept phase is a project specification, as well as a rough technical proposal that provides enough details for the manufacturer and the customer to have a common understanding of the end product.
A typical technical proposal includes:
- One or more 3D concepts
- A preliminary data sheet and block diagrams
- Effort estimates (NRE)
- Budgetary unit cost
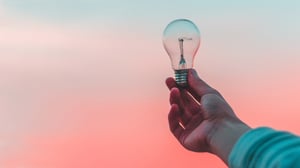
Design
Once the concept is approved, the preliminary data sheet and approved project request is passed on to the Research & Development department. R&D uses this information to create a development charter that is to be signed by all major stakeholders.
Once the development charter is signed, Hatteland’s expert engineers will custom design specialized, embedded systems, displays, and/or I/O options, based on customer dialogue and the specified operational environment, all defined and summarized in the project charter.
The output from this phase is a range of engineering samples, including product blueprints (ES).
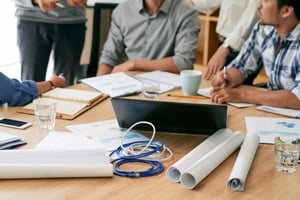
Validation
During the validation phase, project management, in cooperation with multi-site resources from Hatteland Technology’s experienced R&D department, QRTECH, and other partners quality assure and validate the custom product based on tests performed on the engineering samples.
There may be several rounds of ES validation, depending on the findings. Once all requirements are qualified as “PASS”, the final schematics and drawings are released as product blueprints.
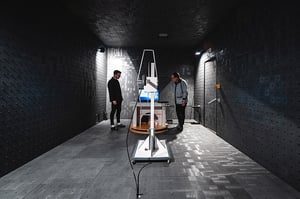
Manufacturing
Following validation, product blueprints are forwarded to our in-house manufacturing facilities, where the product is manufactured and prepared for delivery.
The output of the manufacturing process is the finalized product, accompanied by fully traceable production records and complete SNO control.
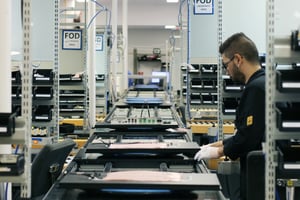
Services
The final phase of Hatteland Technology’s development process is post-delivery services, including change control, EOL/ECN/LTB validation and control, and lifecycle management.
This ensures that the product is manufacturable for a specified period of time and includes engineering changes should components become obsolete, validation of all updates and handling of Last Time Buys on a component or module level. This, in combination with the ability to repair and maintain products throughout the entire production lifecycle, ensures the longevity and stability of the delivery.
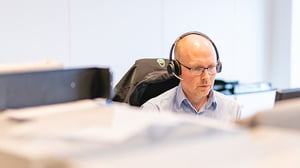