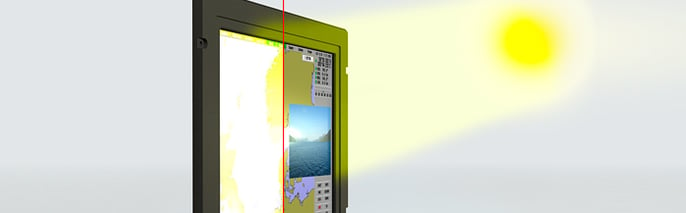
The last decade has seen huge advances in the quality and performance of display screens for marine entertainment systems, navigation, ECDIS, automation and critical naval systems. There is now a high demand for more sophisticated, technically enhanced displays that not only perform under the most extreme conditions, but meet customer expectations in terms of design and view-ability. Hatteland Display's proprietary screen bonding is helping to meet this demand.
A huge breakthrough in the marine displays arena has been the introduction of optical bonding, a process whereby the air gap between the front glass panel and LCD module is filled with a special compound to negate many of the problems related with marine use. A variety of materials may be used within the process, but the development and application of silicone based optical bonding can be attributed to Joseph Sanelle, Hatteland Display's Optical Division manager.
"In the early years of the 1980s, liquid crystal displays were new technology, and optical bonding had limited benefits to the function of the display of the time, the cathode ray tube. CRT screens were dominant and had been well established in most markets setting the standard for all display technologies which developed since. Optical bonding was developed as a critical factor to help make the LCDs equal to the CRTs in visual and environmental performance," explains Sanelle.
While monitors and displays for many industrial and entertainment applications have to withstand heavy usage, marine display manufacturers face some of the toughest challenges: Condensation, salt water exposure, sunlight reflection, night vision, overheating, EMI and form/fit requirements are just some of the factors that must be addressed.
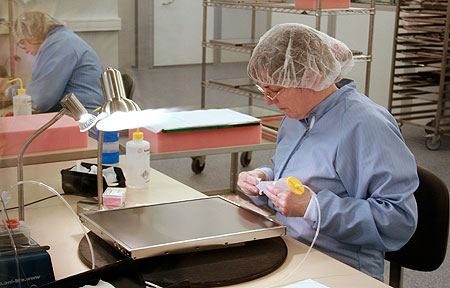
No company could be more committed to overcoming these challenges than Hatteland Display. With 20 years in the marine display and computer business, Hatteland Display has had continuous investment in new technology in order to produce innovative and high quality products. The development of an in-house optical bonding process is no exception to this.
The application of LCD optical bonding to the Marine commercial and yacht product markets was slow to happen compared to the military naval market. Knowing the future growth of the Marine market for new liquid crystal display systems, Knut Vidar Lauritsen launched the program to develop and productize LCD optical bonding in Norway in 2005. Supporting this program development was Joe Sanelle, a chemical engineer from America who first developed optical bonding materials for Tektronix, Inc. in 1983, issued several US & international bonding patents while working for Panelview & White Electronic Designs Corporation (WEDC) in the 1990's, and is a recognized expert in the field of silicone optical bonding of LCD's.
"In the initial stages time had to be spent experimenting & validating unique European materials and related processes to develop, test and prove the new silicon-based materials used in the bonding process," Sanelle comments. "This kind of investment was fundamental to developing a bonding solution unique to Hatteland Display. We now have a proven formula and process methodology that allows any size LCD and glass configuration to be optically bonded with perfect uniformity."
The enhancements from the Hatteland Display optical bonding include much better sunlight viewing (reflection by the sun is reduced by up to 94%), which makes it possible to use cost effective LCD modules not dependant on boosted high brightness and candela values. The filling of the air gap between the TFT and the glass also means that there is no condensation to form, no contamination to be shook loose, and reduced heat build up, which lessens the risk of overheating failure. This is particularly important as the angle that marine displays are often positioned can mean a greater chance of overheating in the first place.
Along with the commitment to research and design, Hatteland Display has a quality system that covers all functional areas and production facilities to ISO-9001:2000 standards, and remains the only marine displays company in the market to manufacture and bond its products in-house. Sanelle concludes: "There are many bonding companies in the world today in addition to Hatteland Display. However, our customers receive a complete product that has been monitored and quality assured under 'one-umbrella' from start to finish, no other company in the market can say it does this."
|