Touch screen, what is coming? |
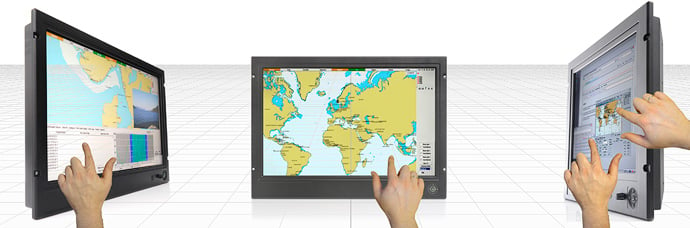 On a general level, all our products are available with the option of having either resistive touch screen or surface capacitive touch screen integrated. Both technologies have been around for many years, availability of sensors is good, and the technical challenges and risks are few. However we are now also exploring and testing with proven new technologies. We have found that Projected Capacitive Touch screen (PCT), widely used with great success on mobile phones and iPAD’s etc, can be equally effective also for marine applications. One of the advantages of PCT is that it has features seen in both resistive and surface capacitive touch screen technologies. The technical benefits of PCT are:- Very good optical performance (same as surface capacitive) - Can be operated with gloves (same as resistive) - Environmentally strong, the touch sensor is inside the product (better than both surface capacitive and resistive) - Supports MULTITOUCH - Strong against rain / drip 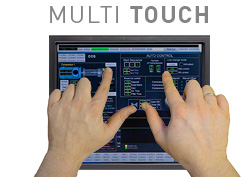 We are currently at a very advanced stage of implementing PCT in our (soon to be launched) smaller size products (8 inch and 13.3 inch), prototypes of which are nearing completion. We expect mass production of these products with the PCT touch option to start in May 2011. Our plan is to then introduce PCT touch technology also in larger size LCD displays. Further information will follow during 2011 via your sales contacts at Hatteland Display, and through future editions of Visions in the coming year. For a broader overview of touch screen technology, some of you may find the following article informative: Touch interfaces are emerging in everything from consumer devices to industrial equipment. Not only because touch is “in fashion”, but also because it provides exceptional and a more intuitive form of human-device interaction. Touch easily can replace simple “low-tech” interfaces such as buttons and switches.
New touch technologies are being created all the time, touch is growing 3x (units) to 10x (revenue) faster than the display industry and projected capacitive touch revenue rocketed from $20 million to $600 million in 3 years.
There is no perfect touch technology. There is more than a dozen of them and each has their own, specific strengths and weaknesses. Different touch applications have various requirements e.g. how many simultaneous touches it needs to support. In reality, the maximum number of touches is just one of more than 40 characteristics that define a touch screen. What really matters is the user experience depending on the interface, application etc. all coming together to work in harmony to do what the user needs.
A well implemented touch interface can be much simpler to use than a conventional mechanical or button-based interface because it can show the user only those controls that are relevant to a particular operation, while all the controls in a conventional interface are always present.
Touch-interface gestures, defined as two-dimensional finger motions, can further simplify an interface and provide an intuitive user experience that goes beyond the typical “button replacement” found in most simple touch interfaces.
Different technologies have different advantages and disadvantages, and there are many to choose from – projected capacitive, surface capacitive, analog and digital resistive, surface acoustic wave, optical, etc. It is important to note that no one touch technology solves all the problems.
It is exceptionally important to plan for sufficient integration testing when developing a touch device, especially when using a capacitive touch sensor. Issues such as RF-EMI affecting the touch sensor, software driver optimizations on the LCD and touch controller, cable-routing, application performance affecting touch responsiveness, unwanted optical interaction between the LCD and the touch sensor, ESD concerns, etc. are quite common. The only way to find and fix these issues is to allow significant time for quality-assurance testing and to have engineers with the right background do the troubleshooting.
Most touch sensors are made of glass, which has many benefits but also adds significant constrains when being integrated into a product. The touch sensor must be integrated correctly to prevent breakage in the event of mechanical stress, to prevent slight deflections of the sensor that could interfere with the sensing baseline, to prevent dust or other contamination from interfering with viewing quality, and to prevent ESD from damaging the touch sensor or system among others. Environmentally sealing the touch screen can be more difficult than sealing just a display, depending on the touch technology.
The future of touch is bright. All possible features create new opportunities for the users, application developers, system integrators and numerous other third parties.
Bibliography Hamblin, M. (2010). Taking Touch to New Frontiers: Why It Make Sense and How to Make It Happen. Information Display , pp. 36-39. Walker, G. (2010). The Best of Times. Information Display , pp. 4-45.
|
|